行业新闻
前沿分析 | 新能源电池外壳行业多种新材料研发应用与市场前景
Date: 2024/1/18 9:28:32
随着动力电池技术线路的不断发展,电池壳成形技术在材料、形状、制造工艺等方面出现了不同的发展路径。为了探讨电池壳成形技术的突破,促进规格和接口尺寸的统一,融入数字化平台,便于集约化生产,打造我国在电池壳成形技术方面的领先地位,恒进展览在3月宁德举办的第五届宁德国际新能源电池与智造技术产业大会期间举行“电池壳体成型与智造技术论坛”。
论坛将以电池壳体设计生产加工制造、装配技术为主题,重点关注设计、铸造、焊接、拧紧装配、测试、整线规划等热点核心工艺和装备技术及发展趋势,探讨新工艺带来的行业变革趋势。
同期大会包括1场全体大会及7场主题专场,预计将吸引来自380+汽车主机厂及电池生产厂家的研发、生产工程技术人员,200+一二级原始设备供应商2500+核心决策人注册参会。
电池是电动汽车最重要的核心部件之一,无论是面对高温、涉水乃至撞击,保护电池的安全都不可忽视。要保护电池的安全,电池的外壳是重中之重。国内地区部分生产企业创新的电池壳体成了保障安全的一大利器!由于电池是电动汽车的核心关键部件,电动汽车研究工作者已经把注意力集中在电动车的电池,并且寻找理想的材料来保护电池。而钢铁是批量生产中最经济和可持续的电池外壳材料。电池壳体如何起到保护作用和电池外壳必须满足的条件是什么?
电池壳体是电动车的必要组成部分,容纳高压电池、电子元件、传感器和连接器,帮助保护车辆的整体结构和安全,使关键部件免受潜在的外力冲击、受热和渗水的影响。纯电动车的电池壳体都比较大,一般长有两米左右,宽一米四左右。这么大的产品要保证防水气密性在技术上是非常有挑战的。一方面在产品设计和制造工艺上国内有的公司采用可以防漏的各种技术,另一方面每一个电池盒产品下线前都要通过严格的气密性检测。同时,电池外壳的主要任务是保护电池模块。它们是驱动系统和结构元件之间的接口,因此是电动汽车中最重要的组件之一。为了确保有效的保护,它必须足够稳定,以在发生事故时保护电池模块不受损坏。内置的冷却系统还可以防止电池模块过热。最后,尽管受到环境影响,电池外壳必须具有极强的抗腐蚀能力,才能保护电池可以正常使用多年。值得一提的是:由于电动汽车充电过程时间较短,电流强度大,使用频率高,所以在保证良好的绝缘性同时还要求电池外壳材料具有一定的耐高温、耐老化性能,并且在燃烧时具有无卤阻燃和低烟密度。热塑与增强塑料材质在电动汽车电池外壳盒子上的制造过程和价值体现分析
相较于金属组件,大面积全塑料外壳既能够缩短循环时间,还有助于减轻车辆重量,从而可以使电动汽车(EVs)的续航里程增加。朗盛(Lanxess)和考泰斯·德事隆集团(Kautex Textron)花了几年时间合作研究电动汽车的电池外壳是否可以由工程热塑性塑料设计和制造。使用直接长纤维热塑性塑料(D-LFT)和聚酰胺6 (PA 6)树脂,他们在可行性研究中开发了一种技术演示器。这项研究系统尺寸为1,400*1,400毫米(长*宽),是一个复杂的大型全塑料外壳,重量在两位数千克范围内。该研究项目的目标是要证明热塑性塑料相较于金属在重量和减少成本、功能综合和电绝缘性能上是很占优势的。考斯特产品研发总监FelixHaas解释道:“作为第一步,我们已经不再使用金属加固结构,同时证明了我们可以商业化生产这些复杂且大型元件”。朗盛电子动力系统项目经理ChristopherHoefs博士补充道:“考斯特和朗盛希望可以利用合作的结果与汽车制造商一起进入批量生产的研发项目”。单阶段制造过程:该演示器是基于C段电动汽车上的电池外壳研制的。它是由带防撞结构的壳体托盘、壳体盖和车底保护装置组成。外壳组件采用单级D-LFT成型工艺生产,而朗盛则优化了杜蕾森B24CMH2.0聚酰胺6 (PA 6)作为模塑料。考斯特将PA6与玻璃纤维粗纱混合用于该工艺。使用朗盛的Tepex dynalite纤维增强热塑性复合材料完成外壳结构的局部加固。Haas解释:“该过程能够缩短周期,因此相比于在钢或铝的加工周期,这种方法更具有经济性”。根据了解获悉,该验证是基于C段电动汽车上的电池外壳研制的。它是由带防撞结构的壳体托盘、壳体盖和车底保护装置组成。如今,高电压电池的外壳最初是由挤压钢或铝材质制成的。取决于车辆类别,外壳的长度可超过2,000毫米,宽度可超过1,500毫米。尺寸、部件数量以及众多的制造和组装步骤使得金属外壳成本非常高。例如,由钢绞线压制型材制成的复杂结构需要很多辅助操作,如焊接、打孔、固定等。此外,在额外的工艺步骤中,必须通过阴极浸涂保护金属部件免受腐蚀。 简化组装和物流:Hoefs说:“另一方面,塑料可以充分设计。通过集成紧固件和热管理组件,电池外壳的单个组件数量可以大大减少。简化了组装和物流工作,从而减少成本”。塑料还具有耐腐蚀性和绝缘性。例如,塑料可以减少系统短路的风险。塑料的低密度和轻质结构可以使外壳重量降低,这有利于增加电动汽车的续航里程。高压电池外壳必须高度满足各种需求。例如,必须坚硬且结实,能够在发生碰撞时吸收大量能量。这是通过机械冲击和挤压试验进行测试的。在汽车起火或碰到电池热失控的情况下,外壳必须是阻燃的。最终,外壳必须集成到车辆结构中。Hoefs说:“我们将在优化元件生产和结构设计上继续努力。我们的目标是以虚拟方式展开工作,在原型试验中节省成本,缩短未来系列元件的上市时间”。与此同时,最近几年来,增强塑料在汽车电池盒中也是关注点超级高,例如SGLCarbon与中国汽车制造商NIO合作开发复合材料电池盒这个事情就能够说明问题,SGLCarbon(德国威斯巴登)宣布,它已与中国汽车制造商NIO合作,为电动汽车开发碳纤维增强塑料(CFRP)原型电池外壳。据称CFK电池盒比传统的铝制或钢制电池盒轻40%,并且与铝相比,具有高刚性和约200倍的导热性。“此外,复合材料在水和气密性以及耐腐蚀性方面也具有最佳值”,西格里复合材料 -纤维和材料业务部门汽车市场部门经理SebastianGrasser表示。箱底和盖子包括夹层芯和几层碳凝胶。用于生产地板和盖子的工具设计是在SGL的轻量级和应用中心开发的,这些部件的碳纤维是在位于美国华盛顿州MosesLake和英国Ord的Muir的SGL工厂生产的。在德国瓦克斯多夫加工成稀松布。SGL在奥地利Riedim Innkreis 的工厂进行了地板和盖子的生产以及各个部件的组装。据说电池的外壳特别轻,稳定且安全。据报道,整个电池盒,包括电池,也可以在三分钟内在NIO自己的交换站更换。西格里碳素公司预计,随着电动汽车的增加,汽车行业电池箱轻量化解决方案的需求将在未来几年内急剧增加。该公司已经与各合作伙伴合作,进一步开发由复合材料制成的不同电池盒,这些电池盒将来可以扩展到各种尺寸和设计的电动汽车电池。“轻量化结构是NIO技术路线图的核心要素之一"。采用复合材料,特别是在电池盒系统中使用高性能碳纤维,我们的车辆提供更好的动态驱动性能,更长的续航里程和非常高的能量密度电池组(超过180Wh / kg)。这些功能非常适合NIO品牌价值,如终极产品和系统效率。为满足更加严苛的排放法规,汽车制造商正致力于开发可规模化生产的动力驱动系统。纯电动、混合动力、插电式混合动力、燃料电池等汽车类型将在未来的汽车市场中发挥越来越重要的作用。但是,目前电动车的续航还尚未达到汽油或柴油车的标准。电动车增加续航的方法一般有两种:一种是安装大容量储能系统,但这会增加车辆重量;另一种是选用高能量密度的储能材料,但是目前电池的能量密度还达不到应用需求。此外,提高车辆整体效率是减少燃料消耗的有效方式。除了上述动力总成中的优化措施外,还需要通过减重来降低行驶阻力,从而实现节能减排。因此,轻量化不仅是燃油车的需求,对电动车来说也非常重要。一般而言,重量减轻100公斤,可减少约10克/公里的二氧化碳排放量,最多可减少0.45升/100公里的油耗。对于电动车,电池包壳体的轻量化不仅可以使汽车高效运行,还将提供更大的续航。但是电池包壳体的设计在轻量化的同时,还需要尽可能地可靠和安全。这就需要考虑其防火安全性、刚性、热管理、电磁兼容性和抗腐蚀性能等诸多因素。当前,电动汽车的电池包壳体主要由铝和钢制成。相比之下,SGLCarbon开发的如图所示的复合材料电池盒可实现40%的减重,其相关机械性能对比如下图。
电池包壳体的底板和上盖的设计对于壳体的性能具有较大的影响。复合材料电池包壳体一般采用三明治结构设计:采用PET、EPDM、泡沫铝等类似的芯层材料,与多层碳纤维或玻璃纤维织物复合材料结合,采用快速固化的树脂材料经模压成型。其中,织物的形式可以是轴向织物、机织物、或者无纺布等,具体如下图。从纤维到预浸料,再到成品的工艺流程如下图所示。同时,材料可以灵活地相互组合以匹配相应的应用需求。特别是沿纤维拉伸方向定位的纺织层具有较好的定性,可较为容易地应用于部件的设计。因此,通过纤维或织物的铺层方向设计可实现不同要求的受力,从而有效地进行材料利用。(1)机械性能:电池包壳体的刚度特别重要,在多数电动汽车中,电池包壳体是车辆结构的重要组成部分,其性能对白车身的整体刚度起着重要作用。这需要电池包壳体满足正碰和侧碰的安全要求。如图,电池包壳体的刚性在很大程度上取决于所使用的三明治结构,一般采用泡沫铝材料作为夹心层材料。此外,纤维增强部件的高比刚度、低重量和良好的阻尼特性也对车辆的噪声、振动、NVH性能具有积极影响。
(2)热管理和阻燃性:复合材料电池包壳体的另一个优势是碳纤维增强复合材料的导热系数比铝合金低200倍,且其具有更好的绝缘性,因此复合材料电池包壳体比传统金属壳体能更好的抵御高低温的性能。目前普遍使用的锂离子电池的理想工作温度在10至40°C之间,一般需要增加冷/热管理系统。而复合材料壳体具有更好的隔热效果,在热条件时所需的能量更少,进一步提高了车辆的效率,降低了总功耗。除了对热管理的积极影响外,低导热系数也是有效阻燃的极佳先决条件。通过添加阻燃剂,复合材料壳体可轻松满足UL94-V-0、UL94-5VB等阻燃要求。 研究人员对样本面板材料进行了比较测试:将样件暴露在距离800℃火焰只有几厘米的地方,测量另一侧温度。由于铝合金在660℃左右的温度下就达到熔点,因此,选择了钢板、标准热固性树脂复合材料和上述添加阻燃剂的三明治复合材料样本进行了测试,结果如图。另一侧的温度分别为:钢:30秒后约为750°C、标准的热固性树脂环氧复合材料:60s后约550°C、添加阻燃剂的三明治结构材料:180s后约350°C。上述结果表明,三明治结构复合材料电池包壳体具有优异的阻燃特性。同时,该材料还具有自熄性,可防止火灾的发生。并且由于热导率低,在发生火灾时,复合材料壳体仅能将电池燃烧产生的高热量有限地传递到相邻部件和乘员舱,这将为乘务人员的逃生赢得宝贵时间。(3)其他性能:此外,SGL Carbon开发的三明治电池包壳体还可以更好地满足防腐蚀性要求,可提供更好的密封性。通过纤维铺层和纤维体积含量的设计,可实现关键区域的电磁屏蔽。同时,复合材料的应用提供了更多集成化设计的空间,相关增强组件、附加元件、连接组件、传感器等都可实现集成化设计。因此,合适的材料用在合适的地方,SGLCarbon通过使用高性能碳纤维复合材料设计开发的三明治电池包壳体减轻了产品质量、提高了系统效率,同时还有助于提升整车的动态驾驶性能,提升续航里程。目前,SGLCarbon已与蔚来汽车合作,为高性能电动汽车开发碳纤维增强塑料电池外壳的原型。未来,SGLCarbon还将与更多的合作伙伴开发不同尺寸、适用于不同电动汽车的复合材料电池包。1.碳纤维电池壳:碳纤维电池壳最大的优势是什么呢?话说SGLCarbon与蔚来汽车合作开发了碳纤维复合材料电池外壳,实现减重40%,想想看多么诱惑人?能够实现减少重量那么多相当于半壁江山了,太划算了,轻量化还降低原材料的采购成本,何乐而不为呢?2.钢制外壳:钢制外壳减少整个生产链中的CO2排放,电动汽车行业的最大挑战之一是以持续不断的可持续发展和环保友好的方式进行生产。的确,电动汽车运行不再需要化石燃料。但是,二氧化碳的排放正在从使用转移到生产。而电池模块及其外壳在这方面起着关键作用。详细的生命周期分析研究结果推荐使用钢材作为电动汽车电池外壳的可持续材料。与铝相比,钢铁成本更低、强度更高,此外,钢铁在生产阶段对环境产生的影响要比铝小得多,与铝制电池盒相比,钢制电池盒生产减少了多达三分之二的温室气体排放。1.福特F-150Lightning搭载麦格纳电池壳体福特全电动F-150Lightning皮卡将于明年春天上市亮相,车型搭载了麦格纳的电池壳体技术,这也是麦格纳在北美市场为福特公司制造的第一批电池壳体。电池壳体的轻量化是一个重要课题。麦格纳的这款铝质壳体有助于极好地控制皮卡电池的附加重量,其铝挤压成型件和冲压成型件采用激光复合焊和冷金属过渡焊接(CMT)方式进行连接,以保证整体的强度。麦格纳正通过车身和底盘的技术专长,引领整个行业的汽车结构设计,为全球客户提供全面的服务和工程解决方案。我们开发钢、铝和多种材料配置的电池壳体,包括轻量化复合材料的电池壳体,以满足每个客户的个性化需求。2.蒂森克虏伯钢铁公司selectrify®电池外壳蒂森克虏伯钢铁公司欧洲的研发团队一直在努力为电动交通的未来问题寻找解决方案。未来,蒂森克虏伯钢铁欧洲将以selectrify®计划的名义,整合其高水平的电动交通材料和应用专业知识,包括轻量化汽车结构解决方案、高度稳定和安全的电池外壳以及由电工钢制成的高效驱动电机及充电桩等。帕特里克·特劳卡(Patrick Tlauka)是蒂森克虏伯钢铁公司selectrify®计划的项目经理,他认为超高强度钢材在电动汽车上的使用具有巨大潜力。作为selectrify®计划的一部分,蒂森克虏伯钢铁公司开发了一种由高强钢制成的电池外壳。除了轻量化和碰撞安全,该电池外壳在防火、电磁兼容性和成本效益方面具有显著优势,可以为电动汽车最敏感和最昂贵的组件——电池提供极佳的安全防护。碰撞安全:Patrick Tlauka说"采用钢材料进行不同设计,我们能够满足广泛的性能要求。能够提供吸收非常高反作用力且几乎不变形的结构概念,也还可以提供具有可吸收冲击能量的缓冲区的软结构概念”。selectrify®电池外壳采用蒂森克虏伯最新开发的钢材设计。蒂森克虏伯的高品质钢铁电池外壳几乎和铝制电池外壳重量一样轻。在减轻车辆重量之余,采用高强度钢制造的多腔室结构的selectrify®电池外壳在侧面碰撞中能够承受非常高的载荷,即使汽车的底盘与异物碰撞,电池外壳也难以变形。防火:坚固耐用的电池外壳绝不仅仅是用于保护电池本身。电池单元的损坏会引起火灾,也可能对乘员造成危险。当今的锂离子电池功能强大,但也经常出现热失控着火现象。铝制电池外壳不能很好地抵抗火焰和高温。在防火测试中,材料仅在30秒后就会坍塌。但是,在紧急情况下,每一秒都是至关重要的。很好的是,即使在电池着火的情况下,钢制电池外壳也能保持远低于其熔点的水平,并能安全地保护乘员。selectrify®电池外壳由高强度钢制成,可确保对电池模块进行全面保护,以防碰撞影响。此保护功能可防止电池起火。在紧急情况下,selectrify®电池外壳提供了几分钟营救时间-这对驾驶员和乘客来说至关重要。降低生产成本:另一个优点是成本低。为了进行分析,假设在七年内每年生产20万辆汽车。计算中包括了材料和生产成本以及零件制造、白车身生产、泄漏测试和腐蚀防护成本的数据。结果显示:selectrify®钢制的电池外壳比铝制的外壳节省了50%的成本。"仅在材料方面,我们就具有很高的成本优势",帕特里克·特劳卡(Patrick Tlauka)将铝制成的电池外壳与selectrify®电池外壳进行了比较:"对于相同的重量,铝的成本是钢的三倍"。展望:高强度钢是稳定的,可以生产出非常薄的壁。这对于电动汽车是决定性的优势,因为如果电池外壳占用的空间较小,则可以给电池提供更大空间。"对于电动汽车而言,更大的电池意味着更大的续航里程”,Tlauka解释道。"电池外壳的薄壁,轻巧和紧凑的设计能够满足许多最终用户的里程焦虑"。selectrify®电池外壳可显着提高电动汽车的防火安全性,生产成本可降低多达50%,并且产生的二氧化碳排放量仅为铝制电池外壳的一半左右。采取这一具有前瞻性的技术为电动汽车制造商改善电动汽车的续航里程和安全性铺平了道路。汽车的核心参数是达到足够的行驶里程。为此,德国马勒公司最新开发了一种集成了热量管理功能的电池盒。这个产品不是通过使用越来越大的电池,而是为提高电池的快速充电能力提供了解决方案。例如,牵引电池可以减少约40%的电量,并且可以快速充电。这样,马勒公司的产品不仅减少了电动汽车的二氧化碳排放量,而且减少了电池生产中全球范围内稀缺原材料的需求。为了能够在快速充电过程中可重复实现必要的高冷却能力,作为马勒电池外壳概念的一部分,电芯被电介质流体直接包围。由纤维增强塑料制成的电池箱结构不仅重量轻,而且非常耐用。由于电池较小,该概念还为电动车辆带来了巨大的重量优势。马勒公司研发高级主管OtmarScharrer博士解释说:“借助新的电池箱概念,马勒公司使电动汽车更经济,更环保,同时保持对客户的吸引力。电池箱不仅生产成本适中,而且减少了昂贵的高性能电池的使用,从而降低了电动汽车成本,使得可以将电动车推向更广阔的市场。”冷却电池和电力电子设备的需求产生了复杂的电路,极大地增加了对单个组件和热管理领域控制的要求。马勒公司从一开始就伴随着动力传动系统电气化和需求的增长,并不断扩展其在研发方面的专业知识.4.Fraunhofer开发由连续纤维增强热塑性塑料组成牵引电池外壳根据了解获悉,Fraunhofer结构耐久性和系统可靠性研究所与合作伙伴开发了一种具有蓄热能力的牵引电池。重点是一种新型的三明治电池外壳由连续纤维增强热塑性塑料(CFRTP),这有助于绝缘热存储在牵引电池预处理。在柴油汽车和一般内燃机(ICE)汽车即将被禁止的时代,电池电动汽车(BEV)正变得越来越令人感兴趣,特别是在城市环境中。提高电池容量可以延长行驶时间,但电动汽车的驱动范围会有所不同,特别是在较低的环境温度下。因此,在欧盟项目“优化能源管理和使用”(OPTEMUS)范围内,开发了大量提高效率的技术,并将其整体联系起来,特别是为了减少菲亚特500eEV的范围变化。这包括具有蓄热能力的牵引电池,该电池是弗劳恩霍夫结构耐久性和系统可靠性研究所与合作伙伴共同开发的。重点是一种新型的三明治电池外壳由连续纤维增强热塑性塑料(CFRTP),这有助于绝缘热存储在牵引电池预处理。在Fraunhofer LBF开发的一种混合原位工艺可在成本敏感的大容量应用中生产复杂的、功能集成的CFRTP三明治元件。Fraunhofer LBF开发的蓄热材料可用于在乘车前在寒冷天气中对温度敏感的电池进行预处理,并使用隔热的CFRTP夹心外壳使其保持在最佳工作温度。因此,通常可以避免主动温度控制。相反,可以缓解电池在快速充电过程中可能出现的短期、不必要的热量增加。“我们开发的材料、结构和工艺技术为驾驶员提供了更可靠和一致的Bev范围”。此外,在Fraunhofer LBF负责研究项目的Felix Weidmann解释说:“此外,车辆开发人员和设计人员还可以从轻量级结构和功能集成的新工艺技术中获益”。机械和热的要求是由新型CFRTP电池外壳提供的。这是由一个三明治结构的基础上UD磁带面片(UDMAX,SABIC)覆盖一个完整的聚合物泡沫核心。泡沫芯子提供了隔热材料,而面板承担了大部分的负荷。为此,LBF的科学家将UD磁带整合成一种交叉复合材料,并将其预成三维(3D)复合面片。在这些三维面片之间,聚合物泡沫芯体采用一种新的混合原位制造工艺注塑成型。由此产生的三明治结构有几个优点:它提供了高的轻量化潜力,并实现了高比弯曲性能和抗冲击性能。此外,它还提供了针对入侵事件的高级别保护,入侵事件尤其是在电池组中发挥着重要的安全作用。电池模组外壳由隔热聚合物泡沫(黑色)组成,表面覆盖连续纤维增强(CFRTP)面片,使用混合原位工艺仅需2分钟即可制造出电池组件外壳。为了满足汽车的要求,材料和结构的概念已经发展到大容量的应用。OPTEMUS电池外壳的制造是由Fraunhofer LBF开发的一种混合制造工艺实现的,这使得首次能够在短短2分钟内提供具有功能集成和隔热的CFRTP三明治组件。5.朗盛工程塑料和INFAC共同开发新型EV电池模块外壳电池外壳使用朗盛的DurethanBKV30FN04,以满足最新电动汽车组件的严格机械和化学性能要求。无卤、阻燃和玻璃纤维增强的PA6具有优异的阻燃和电气性能。该材料具有高度的可加工性,能够集成外壳组件所需的复杂功能,从而减少零件数量、简化组装过程并减轻重量。韩国整车厂推出的EV车型的量产采用了新的电池外壳部件。“电池外壳量产的成功证明了朗盛Durethan材料在电动汽车电池方面的卓越表现,其中技术和安全至关重要”。我们的高性能塑料将为电动汽车和电池市场做出重大贡献,”朗盛亚太区高性能材料 (HPM) 业务部门负责人Milan Vignjevic 表示"。英法克朗盛工程塑料公司与韩国汽车零部件供应商INFAC共同开发了用于电动汽车(EV)的电池模块外壳。该电池外壳已用于韩国OEM推出的EV车型的量产。
具有优良机械和电气性能的阻燃塑料:对于电池模块外壳,减震和热管理至关重要,这些特性保护电池免受外部冲击。DurethanBKV30FN04不仅机械坚固,而且具有高压绝缘性,可耐受高达800 V的电压并有效阻断高压电流。具有很强的阻燃性能,可在发生火灾时防止或延迟火焰蔓延。玻璃纤维增强的DurethanBKV30FN04对机械负载的耐久性优于未填充的PA6。此外,它在与电解质或冷却介质接触时保持出色的强度和刚度,并具有耐化学性以抑制化学诱导的损坏。朗盛的工程塑料可应用于各种电池组件,包括电池盖、高压连接器、电缆支架和电池冷却系统管道以及氢燃料电池汽车的零件,如储氢罐。它还可以替代各种部件中的金属,实现轻量化设计。它允许在一个过程中生产多个功能组件,这是下一代移动市场需求持续增长的驱动因素,其中许多技术和组件开始发挥作用。“朗盛的优质材料、技术专长和定制工程服务使我们能够加快发展。这有助于巩固我们在快速发展的电动汽车电池零部件市场中的地位",INFAC采购与开发主管Gyuso Lee说。韩国HPM负责人Sanghun Han表示:“朗盛与包括韩国在内的全球领先的汽车原始设备制造商密切合作。这就是为什么我们能够在早期阶段识别电动汽车的趋势和挑战,并参与各种电动汽车和电池开发项目。凭借与客户积累的成功案例,我们正在将自己打造成新型移动出行领域的关键材料合作伙伴"。汽车行业在全球范围内都处于剧烈变革之中。可供选择的驱动技术,新的连接模式和自动驾驶都需要全新的汽车设计概念。科思创公司目前关注的焦点之一是在电动汽车中使用聚碳酸酯塑料。未来电动汽车和混合动力汽车的核心是锂离子电池。为了精确地在小空间中放置大量的电池单元,电池座和电池支架以及外壳组件必须具有非常强大的尺寸稳定性及高度的机械坚固性。根据电池组的设计原理,该材料还必须具有阻燃性,此外,即使是在壁厚低至0.75毫米的情况下,也要符合美国保险商试验所(UnderwriterLaboratories Inc.)的UL94可燃等级的V-0级。用于电池外壳的高性能塑料解决方案如下:科思创在笔记本电脑和其他电子设备的封装锂离子电池方面拥有多年经验。为实现这一目标,该公司开发了多种聚碳酸酯混合物,不仅符合上述要求,而且在广泛的温度范围内,特别是在零下温度下,也具有极强的抗冲击能力。在2018年德国塑料工业贸易展会(Fakuma 2018)上,该公司将在B4展厅的4206号展台展示各种电池模块,电池座,碰撞吸收器和其他产品。科思创的JulianMarschewski博士解释道:“当涉及到电池座和电池集成模块时,防火保护尤为重要。”电动汽车专家补充说:“电池周围使用的材料的性能,对于成品部件来说,在许多功能性和安全性测试中都起着决定性作用,并且有助于电池在整个使用寿命周期内的安全运行”。定制材料:Bayblend®FR型阻燃聚碳酸酯ABS(丙烯腈-丁二烯-苯乙烯)混合物是电池座和电池模块的理想材料。该材料具有耐热性和尺寸稳定性,使用该材料可通过注塑成型工艺高效生产部件。该材料还用于柏林制造商GreenPack的移动充电电池。将于Fakuma 2018展会上展出的碰撞吸收器由PC-PBT(聚对苯二甲酸丁二醇酯)Makroblend®KU-27912/4制成。该材料具有非常高的抗冲击性强度,并且在低温下具有特别高的延展性。蜂窝状结构使得这种碰撞吸收器具有极强的抗冲击性能。另一种特殊材料Makrolon®TC产品系列的高填充聚碳酸酯材料,已经应用于LED灯的散热片。这类产品具有导热性,但也作为电绝缘产品使用,因此它们有助于实现高效的电池热管理。适用于恶劣环境的电池组:Enduros车型必须为大风和各种天气条件做好准备,但最重要的是必须承受最严苛的力学性能要求。在这些越野摩托车型中,趋势也是电力驱动。加州电动自行车专家AltaMotors是这类器械的领先制造商。品牌名为Alta Pack的电池就配备了护套,该护套由具有极强抗冲击性的PC-PBT混合物Makroblend®制成。预计,复合材料在新能源电池壳领域的应用前景依然十分看好,大家知道电池壳乃是新能源汽车中的纯增量零部件,单车价值量约3000元左右。电池壳主要由上盖与下壳体组成,是动力电池模组的“骨架”,用来保护电池PACK抵抗外界冲击、防尘防水等等。电动汽车的电池封装外壳(也称为电池槽、盒或外壳)主要用来包装和保护电池。它们的形状和大小各不相同,并且正如其他汽车部件一样,在用材方面可有多种选择,不同材料间的竞争也较为激烈。电池壳带给电动车难题: 电动汽车的里程焦虑如下!里程焦虑一直是新能源汽车的头痛点,无论哪个新车的上市,极限里程挑战都是其必过难关。降低重量是提高里程续航的方案之一。一般认为纯电动汽车重量降低10%,续航里程便可增加约6%。新能源汽车“三电”系统约占整车整备质量的1/4左右,有数据显示,在传统汽车基础上设计的新能源汽车比传统燃油车质量会增加15%以上,所以轻量化是新能源汽车比传统汽车更需要的课题。在动力电池系统中,电池壳占系统总重量约20-30%,是主要结构件,显著影响其电耗、动力性、制动性能、被动安全性、一次充电续航里程等,因此新能源汽车电池壳的轻量化显得更为重要。轻量化离不开高强度钢、镁铝合金、高性能塑料和碳纤维复合材料等轻量化材料的应用。要知道:碳纤维电池壳的特性与优势会在电动汽车应用领域大放异彩,因为碳纤维电池壳可以改善隔热保温性,降低噪音,减少振动,同时降低声振粗糙度。◆减轻重量:如果电池外壳由100%的复合材料而不是铝制成,则车体重大最多可减轻40%。由于电池盒因素导致车体重量减轻,因此在牵引较轻的车辆时,所需的电池和发动机尺寸都会减小。这种积极的螺旋效应可降低车辆成本和里程焦虑,有助于大力促进电动汽车的规模化使用。◆隔热性:复合材料除了材质较轻的特质外,还避免了对单独隔热系统的需求,这进一步减轻了车体重量,有助于精简供应链和价值链。对于金属电池封装外壳,需要在材料周围加装隔热保温系统,以保持电池的工作温度。由于复合材料具有隔热保温特性,在防止传热方面有着很好的效果,因此无需在系统中加装更多的增重部件。◆噪音、振动和声振粗糙度:相对于金属材料而言,复合材料的噪声、振动和声振粗糙度(NVH)较小,因为它们具有固有的阻尼特性。这对于电池封装外壳和其它车辆部件而言都是如此,两者的差异性可能意味着在驾驶体验方面,一个更豪华舒适,而另一个舒适度要差一些。◆安全性:从更大的车身来看,复合材料电池外壳可以设计为车身结构的一部分,不仅可以保护电池,还可以保护车辆中的乘客。复合材料的强度和刚度特性超过了铝或钢,从而能够提供更好的碰撞安全性。这种结合将需要电池封装外壳供应商和底盘设计者之间的密切合作,但对于提高车辆安全性而言,的确是切实可行的。近期推出的复合材料电池解决方案如下:回顾2021年的时候帝人集团旗下的大陆结构塑料公司(CSP)推出了几种新的先进复合材料配方,这些配方在可燃性、热失控和VOC排放方面满足最严格的电动汽车电池外壳性能标准,同时提供片状模塑料(SMC)的设计灵活性。这些新型复合材料包括低VOC配方、ATH填充系统、膨胀系统和酚醛系统。再者,2021年5月,碳纤维制造商东丽工业(日本东京)宣布开发出一种高导热技术将碳纤维增强塑料(CFRP) 的散热性能提升至金属的散热性能。将此技术应用于 CFRP 可通过材料内部的热传导路径有效地从其来源散发热量。这有助于抑制移动应用中的电池退化,同时提高电子设备应用中的性能。2021年10月,弗劳恩霍夫LBF宣布开发出一种用于电池电动汽车的低成本轻质电池壳,与铝电池壳相比,它可减轻40%的质量。虽然该部件使用了纤维增强复合材料,但其成本却较低,这是因为使用了一种特别开发的高效生产工艺,同时采用了应力等效结构设计。由弗劳恩霍夫LBF的研究人员组成的团队,利用他们在该领域的专业知识,采用连续纤维增强热塑性塑料以及结合了高效发泡注射成型与CFRTP的创新工艺,生产出一种采用三维夹层设计的轻量化电池壳。赢创工业集团(德国埃森)去年也在报告说,它正在领导一个合作伙伴联盟,该联盟使用玻璃纤维增强的环氧树脂片状模塑料(SMC)为电动汽车解决方案开发了一个更轻、更经济的高压电池外壳概念。该整体电池系统概念旨在为汽车行业提供一个更安全、更节能的金属或价格更高的碳纤维增强塑料(CFRP)的替代品。2022年4月,巴斯夫和一级供应商 L&L Products 为福特2022 F-150Lightning 开发了电池保护解决方案。该团队在不影响强度的情况下减小了电池系统中的横梁尺寸。横梁是设计用于承受高负载的结构部分,可确保电池和乘员在车辆中的安全。CCS 将纤维增强拉挤复合材料载体与高度工程化的密封剂和粘合剂组合成平面轮廓。这个过程产生了用连续纤维和垫子加固的直线或弯曲的复合型材。石墨和碳纤维复合材料供应商西格里(SGL Carbon)在5月份巴黎JEC复合材料展览会上展示其针对电动汽车电池盒的复合材料解决方案。据介绍,西格里正改善轻质结构的碳纤维在生产过程中的堆栈自动化,减少材料浪费来节约资源,减少碳纤维的碳排放。根据了解获悉,采用西格里碳纤维复合材料制成的电池外壳,可比响应的钢材外壳减轻50%的重量,它在耐火性、刚性、声学以及热屏蔽、电磁屏蔽方面的性能均能满足汽车相应的要求。借助碳纤维复合材料,传感器可集成用于检测电动汽车底部的损坏情况。总结:轻量化是现在和未来汽车行业的一大趋势,包括电池外壳将在2025年前后依然前景看好,轻量化材料将替代过去更多笨重的材料是必然发展趋势。根据外媒报道,目前,一些公司正在竞相开发相关的商业解决方案。例如,德国特种化学品公司朗盛(Lanxess)和汽车零部件供应商考泰斯·德事隆(Kautex Textron)正在对直接长纤维热塑性塑料(D-LFT)和聚酰胺6(PA 6)树脂进行可行性研究。与此同时,西班牙塑料技术研究所(Aimplas)利用可重复使用、可回收的长纤维热塑性复合材料,开发用于轻型车辆的可持续结构电池外壳,使放电后的电池组可热插拔。在其他方面,Vestaro联盟采用一种新颖的方法,将轻质薄板模压化合物用于高压电池模块外壳。祝福该产业未来更加辉煌夺目,拭目以待。材料轻量化是目前汽车轻量化技术的主要途径,从实际应用上看,高强度的复合材料是汽车材料轻量化的理想材料。汽车车身的轻量化与材料轻量化的发展方向保持一致,传统的车身以钢铁为主,占汽车质量的30%~40%,如果将部分零件替换为镁铝合金,甚至是碳纤维等高强度复合材料,那汽车减重的效果会更加可观,随着近几年新能源汽车的迅猛发展,汽车电池系统增重明显,各大汽车厂商将整车轻量化作为重点研究目标,推动了复合材料的快速发展。未来,高分子复合材料的发展将面临着以下挑战:在环保方面,需加快研究复合材料可循环使用技术,提高复合材料的再利用率,降低环境污染,实现资源的可持续发展;在性能方面,为了弥补单一增强体复合材料的性能不足,可以向多尺度增强体复合材料的方向拓展,使复合材料在汽车上的应用更加多元化;在整体发展方面,复合材料的发展需要整个汽车产业链的一体化协同发展,包括材料、加工工艺、模具、设计、设备、试验等方面,形成产学研合作的技术创新体系,技术提升发展的空间很大。EV Battery Housing Design & Manufacturing Expo 2024 上海电池壳体设计与制造装备展是AMTS 2024主题展之一,将于2024年7月3-5日在上海新国际博览中心举办。
展会依托于上海国际汽车制造技术与装备及材料展览会(AMTS)在汽车研发、设计、制造前端市场20年的人气和产业资源积累,紧跟市场行业发展及市场需求,汇聚全球顶尖的电池壳体设计生产企业,电池壳体制造装备生产商、一二级供应商,通过一站式展览展示最新的电池壳体材料、制造工艺与装备、电池壳体创新设计方案与产品。为电池壳体产业与电池生厂及电池PACK集成厂家研发与制造工程技术人员提供一站式商贸及交流平台。
展示范围包含:电池壳体产品(电芯壳体、电池上壳体、电池托盘);电池壳体材料(复核材料、高强度钢、铝合金材料);开发设计技术与装备(CAE仿真技术、3D打印设备);壳体成型工艺与装备(压铸设备、挤压成型设备、机加设备、检测设备、清洗设备);连接工艺与装备(焊接设备、FDS设备、涂胶设备);动化产线系统集成解决方案。
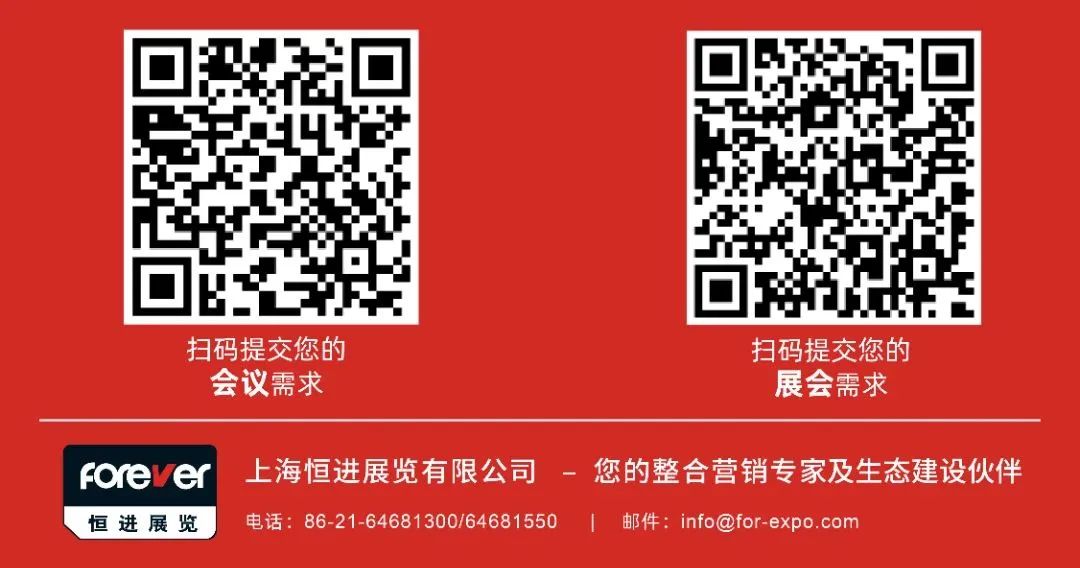
参会咨询:
电话:86-21-64681300
邮箱:info@for-expo.com